هلدینگ فاخر به منظور ایجاد اکوسیستم فاخر در حوزه های لجستیک، تجارت الکترونیک، تولید و بازرگانی و با ماموریت شکلدهی و راهبری اکوسیستم فاخر با نوآوری و توسعهی شبکه ارزش در بازار هدف شکل گرفته است.
کاهش هزینه در زنجیره تأمین
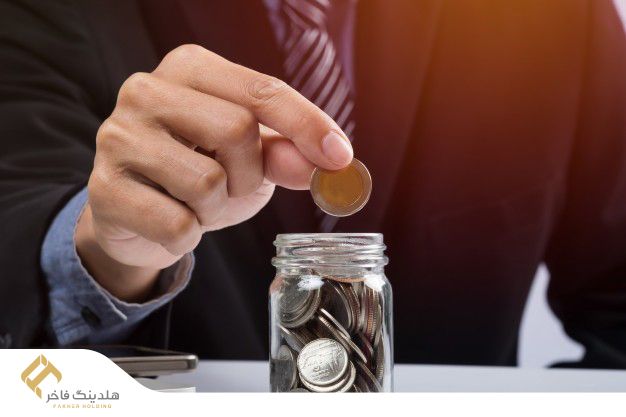
سودآوریِ فعالیت شرکتها تا حد زیادی به کاهش هزینههای لجستیکی آنها بستگی دارد و به همین دلیل، شرکتهای زیادی تلاش میکنند تا با انجام بازنگریهای مستمر در زنجیرههای تأمین، کارایی عملیاتی و متعاقباً حاشیه سودشان را افزایش دهند. اما چطور میتوان چنین کاری انجام داد؟
در این مطلب قصد داریم چالشهای پیش روی چهار شرکت معروف دنیا در کاهش هزینههای لجستیکی را بررسی کنیم و ببینیم که این شرکتها چه راهکارهایی را برای حل این چالشها اتخاذ کردند؟ اگر شما هم درصدد این هستید که هزینههای لجستیکی شرکتتان را کم کنید، مطالعه این مطلب میتواند ایدههای ارزشمندی را به ذهنتان متبادر کند. پس بدون فوت وقت برویم سراغ معرفی این چهار شرکت!
یک. Deere and Company
شرکت Deere and Company طیف متنوعی از محصولات را تولید میکند که ترکیبی از ماشینآلات کشاورزی سنگین و همینطور تجهیزات صنعتی را که بهصورت سفارشی ساخته میشوند، در برمیگیرد. خردهفروشی محصولات این شرکت، وابستگی بسیار زیادی به فصول سال دارد و بیشترین میزان فروش بین ماههای مارس و ژوئیه اتفاق میافتد.
شرکت Deere and Company از طریق ارسال مستقیم و عملیات کراس داکینگ (Cross Docking) از انبارهای واقعشده در نزدیکی تأسیسات تولیدی شرکت، انبار موجودی فروشندگان را پُر میکرد. این سازوکار بسیار پرهزینه و درعینحال کُند بود و شرکت به همین دلیل، تدوین و پیادهسازی پلنی را برای کاهش هزینههای لجستیکی در دستور کار قرار داد تا بتواند ظرف چهار سال، 10% از هزینهها را کاهش دهد.
این شرکت با بررسی شبکه زنجیره تأمین، آن را بازطراحی کرد که این امر به راهاندازی مراکز عملیاتیِ میانی (بین مبادی تا مقاصد) و بهینهسازی مکانی ترمینالهای کراس داک منجر شد. ادغام محمولهها و ارسال آنها از طریق ترمینالهای بزرگ در فصول اوج فروش، از دیگر اقدامات این شرکت برای کاهش هزینههای لجستیکی بود. علاوه بر این، شرکت همکاریاش را با ارائهدهندگان خدمات لجستیک شخص ثالث افزایش داد و توانست بهواسطه این همکاریها، یک شبکه لجستیکی اثربخش بسازد که در هر زمان میتوانست متناسب با نیاز و شرایط، نسبت به بهینهسازی آن اقدام کند.
این شرکت توانست ضمن کاهش 1 میلیارد دلاری هزینه نگهداری موجودی، زمان تحویل به مشتریانش را نیز از 10 روز به 5 روز و بعضاً کمتر برساند و در هزینههای سالانه حملونقل نیز 5% صرفهجویی کند.
دو. Intel
شرکت اینتل که قطعاً نیازی هم به معرفی ندارد، پس از عرضه تراشههای ارزانقیمت Atom در جستجوی راهی برای کاهش هزینههای لجستیکی بود. متوسط هزینه لجستیکی 5.5 دلار برای تراشههای 100 دلاری، قابلقبول بود اما برای تراشههای جدیدی که فقط 20 دلار قیمت داشتند، زیاد به نظر میرسید. ازآنجاییکه هر محصول Atom یک جزء مستقل بود، هیچ راهی برای کاهش هزینههای گمرکی آن وجود نداشت. این شرکت قبلاً هزینههای بستهبندی را نیز به حداقل رسانده بود و با بالاترین نسبت ارزش به وزن، نمیتوانست هزینه توزیع تراشهها را بیشتر از این کاهش دهد. اینتل برای کاهش هزینههای لجستیکی فقط یک راه داشت و آن هم کاهش هزینه نگهداری موجودی بود. سطح موجودی این شرکت برای پشتیبانی مطمئن از چرخه سفارشهای نُههفتهای، بسیار بالا بود. بنابراین چاره کار، تقلیل سطح موجودی کالا از طریق کاهش زمان چرخه سفارش بود.
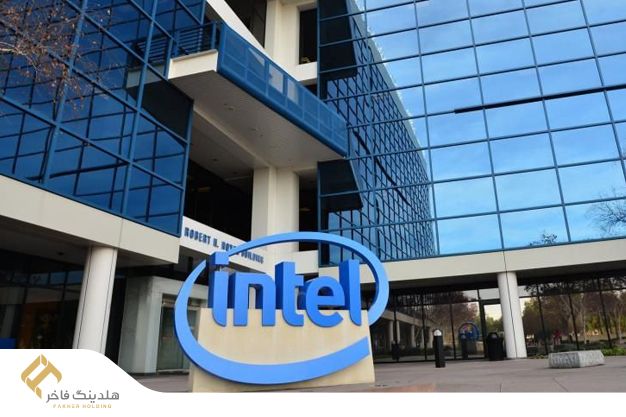
اینتل تصمیم گرفت از استراتژی مورداستفاده در صنعت نیمههادی استفاده کند که همان ساخت طبق سفارش (Make to order) بود و این ایده را از طریق استقرار یک واحد تولیدی در کشور مالزی عملی کرد. با استفاده از نوعی فرایند مکرر، شرکت بهتدریج توانست ناکارآمدیهای زنجیره تأمین را شناسایی و رفع کند و بهاینترتیب، زمان چرخه سفارش را مستمراً کاهش دهد.
سرانجام اینتل با رویکردی تدریجی، توانست زمان چرخه سفارش تراشه Atom را از 9 هفته به 2 هفته تقلیل دهد و اینگونه بود که هزینه متوسط لجستیکی برای این تراشههای 20 دلاری را بیش از 4 دلار کاهش داد.
سه. Starbucks
حتی غول کافیشاپ دنیا یعنی استارباکس هم طی سالهای 2006 و 2007 مشکلاتی جدی را در تأمین اقلام موردنیاز 16700 شعبهاش در سراسر دنیا تجربه کرد و درصدد کاهش هزینههای لجستیکی برآمد. سران این شرکت با بررسی عملکرد زنجیرههای تأمین، دریافتند که عملکرد این زنجیرهها با آنچه انتظار میرود، اختلاف زیادی دارد. آنها حین ارزیابی سازوکار لجستیک شرکت، مشکلات زیر را شناسایی کردند:
- عدم تحویل بهموقع بیش از 50% محمولههای توزیعی
- هزینه سرسامآور لجستیک شخص ثالث بهواسطه اتخاذ تصمیمات ضعیف در امر برونسپاری
- زنجیره تأمین شرکت مانند بسیاری از سازمانهای جهانی بیش از آنکه بر مبنای طراحی و نیازسنجی دقیق ایجاد شده باشد، بر مبنای اقدامات اقتضایی تکامل پیدا کرده بود و همین امر به پیچیدگی غیرضروری و بیشازحد آن منجر شده بود.
رهبران استارباکس سازماندهی مجدد زنجیره تأمین، کاهش هزینههای لجستیکی، بهبود خدمات و فراهمسازی بستری برای بهبود زنجیره تأمین در آینده را بهعنوان اهداف اصلی شرکت تعیین کردند. آنها برای نیل به این اهداف، وظایف زنجیره تأمین را به سه دسته اصلی یعنی برنامهریزی، ساخت و تحویل تقسیم کردند. علاوه بر این، با افتتاح یک مرکز تولید جدید، تعداد کل مراکز تولیدی در آمریکا را به چهار مرکز رساندند. در مرحله بعد، استارباکس به شراکتش با همه شرکتهای لجستیک شخص ثالث غیر از آنهایی که عملکرد واقعاً مؤثری داشتند، خاتمه داد و عملکرد شرکای باقیمانده را از طریق یک سیستم کارت امتیازی هفتگی با در نظر گرفتن توافقنامههای جدید در سطح خدمات، تحت نظارت و مدیریت قرار داد. با استناد به اظهارات پیتر گیبونز، معاون اجرایی زنجیره تأمین جهانی در آن زمان، استارباکس توانست تا پایان برنامه تحولش و بهواسطه کاهش هزینههای لجستیکی، بیش از 500 میلیون دلار صرفهجویی کند.
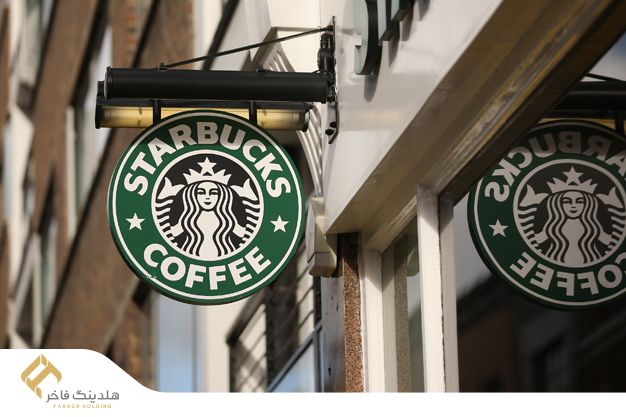
چهار. AGCO
از دیگر نمونههای موفق در کاهش هزینههای لجستیکی، شرکت AGCO است که مثل شرکت Deere and Company نامی پرآوازه در حوزه تولید و عرضه ماشینآلات کشاورزی محسوب میشود. این شرکت بهموازات رشد و توسعه با افزایش پیچیدگی زنجیره تأمین محصولاتش مواجه شد. این پیچیدگی طبیعتاً با افزایش هزینه همراه بود اما شرکت تا چند سال، توجه زیادی به این مسئله نشان نمیداد که البته مهمترین دلیل این امر، ماهیت پراکنده و غیرمتمرکز شبکه جهانی آن بود. سرانجام رهبران AGCO در سال 2012 به این نتیجه رسیدند که این وضعیت نمیتواند ادامه پیدا کند و باید برای کاهش هزینههای لجستیکی و بهینهسازی استراتژیک زنجیرههای تأمینشان، شیوه جدیدی اتخاذ کنند.
شرکت AGCO سبد محصولات گستردهای دارد زیرا پنج برند مجزا زیرمجموعه آن هستند. قبل از آغاز برنامه بهینهسازی، تأمین منابع و عملیات لجستیک داخلی شرکت توسط تیمهایی که در کشورهای مختلف مستقر بودند، انجام میشد. این تیمها کارایی و عملکرد همسطحی از حیث مدیریت زنجیره تأمین نداشتند و عملیات را با استفاده از ابزارها و سیستمهای مختلف انجام میدادند. همین ناهمسانی و چندپارگی باعث میشد که زنجیره تأمین AGCO فاقد انسجام و شفافیت لازم باشد و شرکت نتواند از مزایای همافزایی و صرفهجویی به مقیاس استفاده کند.
این شرکت بعد از ارزیابی عملکرد زنجیره تأمین با استفاده از مدل SCOR تصمیم گرفت از یک فناوری جدید در قالب یک سیستم یکپارچه و جهانیِ مدیریت حملونقل استفاده کند و در کنار آن از طریق مشارکت با یک شرکت توانمند در حوزه تدارکات شخص ثالث، ضمن کاهش هزینههای لجستیکی، به کارایی عملیاتی مدنظرش دست پیدا کند.
ازآنجاییکه واحدهای مستقر شرکت AGCO در آمریکای جنوبی و شمالی، مدتی قبل از اتخاذ این تصمیم با همین سیستم جدید مدیریت حملونقل کار میکردند، رهبران شرکت تصمیم گرفتند این مدل را در اروپا نیز تکرار کنند و در صورت موفقیت، آن را به سایر مناطق عملیاتی شرکت نیز توسعه دهند. با استفاده از این فناوری، یک برج مراقبت لجستیک ایجاد شد که از طریق آن، همه فعالیتهای روزانهی تأمین داخلی در اروپا از مذاکره برای نرخ حمل بار تا صدور خودکار صورتحساب، یکپارچه و هماهنگ میشد.
کاهش هزینههای لجستیکی به میزان 18%، دستاورد خیرهکننده شرکت AGCO از اجرای برنامه بهینهسازیاش بود. از زمان ارائه و اجرایی کردن مدل عملیاتی جدید در چین و آمریکای شمالی، این شرکت ضمن کاهش 28 درصدی هزینه تدارکات و تقلیل 25 درصدی سطح موجودی، عملکرد شبکهاش را نیز 25% بهبود داده است.
سخن آخر
کاهش هزینههای لجستیکی از اهداف اصلی شرکتهای مختلف است و در این گفتار دیدیم که چهار شرکت بزرگ جهانی چطور توانستند با بررسی زنجیرههای تأمینشان، به این هدف نائل شوند. البته غیر از شرکتهای مذکور، شرکتهای دیگری هم هستند که نمونههای موفقی در کاهش هزینههای زنجیره تأمین محسوب میشوند که در این خصوص میتوان از Terex، Avaya و Sunsweet Growers نام برد.
عملکرد شرکتهایی که در زمینه کاهش هزینههای لجستیکی موفق عمل کردند، میتواند چراغ راه شرکتهای کوچکتر باشد. برای کاهش هزینهها در این حوزه، باید بررسی کاملی از زنجیره تأمین داشته باشید و حلقه معیوب زنجیره را شناسایی کنید. معمولاً بخش عمدهای از مشکلات، از یک عامل اصلی مثل استراتژی نامناسب، شرکای تجاری ناکارآمد، ساختار شبکه و ... ناشی میشوند که با شناسایی و بهبود آن عامل میتوانید، تغییرات مثبتی را در عملیات لجستیکی شرکت ایجاد کنید.
مطلبی دیگر از این انتشارات
روندهای آینده صنعت لجستیک
مطلبی دیگر از این انتشارات
رضایت مشتری؛ مزیت رقابتی در صنعت لجستیک
مطلبی دیگر از این انتشارات
ویژگیهای موردنیاز رهبران سازمانی در زمان همهگیری کووید-19 (به همراه نسخه صوتی)