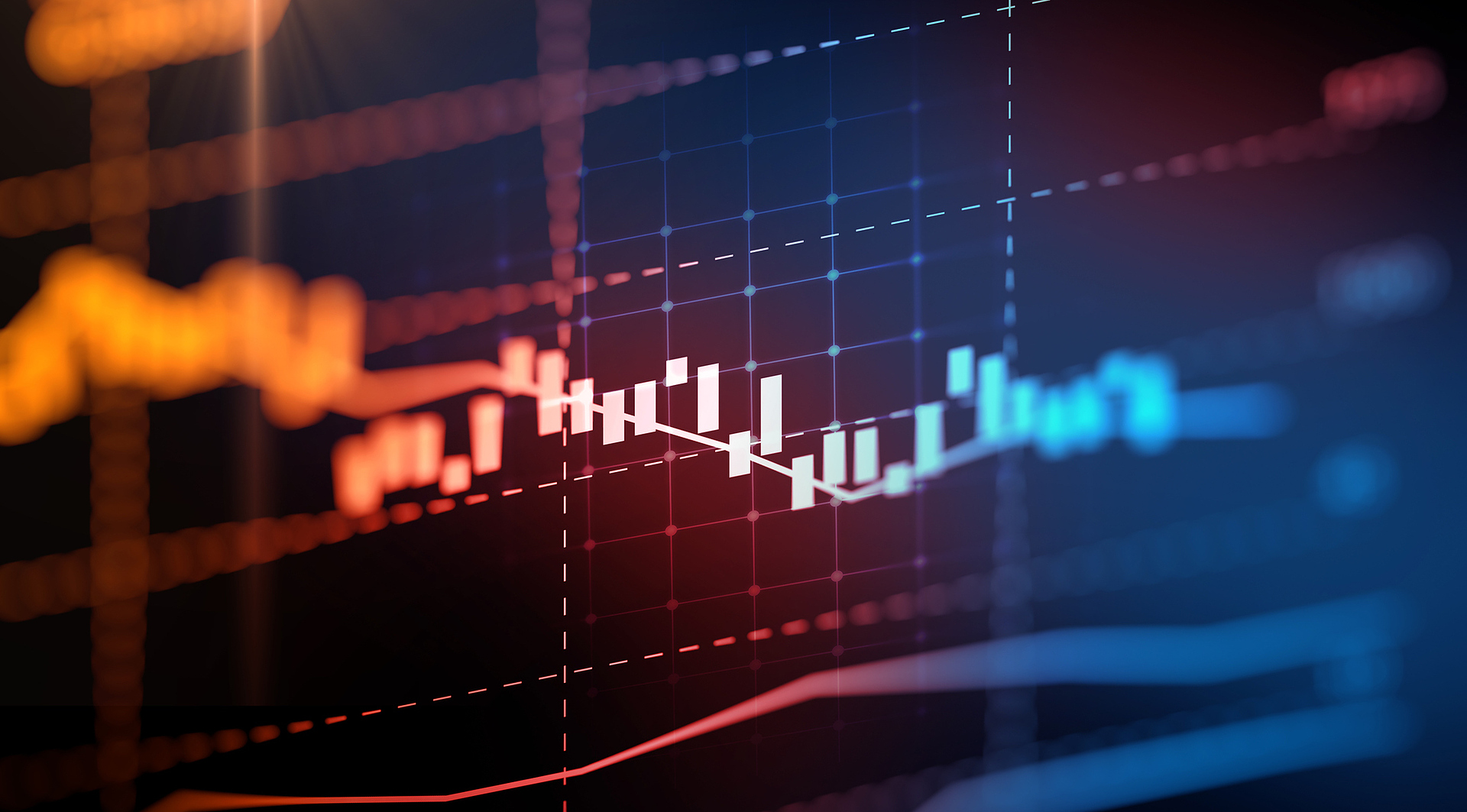
دانش اقتصاد و انتظارات
خواندن ۲ دقیقه
تولیدکننده چرخ دنده و چرخ زنجير انتظارات خود را از رئیس برنامه ریزی و کنترل تولید چنین بیان کرده است.
شرکت کولیس در شهرک صنعتی سهند واقع است و دارای سرویس رفت و آمد است.
علاقه مندان می توانند رزومه خود را به cv@coulisseco.com یا در واتساپ به شماره 9911151246 ارسال نمایند.
cv@coulisseco.com
برنامه ریزی مواد اولیه (MRP) یکی از سیستم های مهم در مدیریت تولید و زنجیره تامین است که به سازمان ها کمک می کند تا منابع خود را بهینه سازی کنند و فرایند تولید را بهبود بخشند. هدف اصلی MRP، اطمینان از این است که مواد اولیه و قطعات مورد نیاز در زمان مناسب و به مقدار کافی در دسترس باشند تا تولید بدون وقفه ادامه یابد.
در ابتدا، MRP با استفاده از اطلاعاتی مانند پیش بینی تقاضا، لیست مواد اولیه و زمان بندی تولید، یک برنامه ریزی دقیق برای تامین مواد اولیه انجام می دهد. این سیستم به طور خاص برای مدیریت موجودی ها طراحی شده است و به شرکت ها اجازه می دهد تا موجودی های خود را کاهش دهند و در عین حال از کمبود مواد اولیه جلوگیری کنند.
یکی از جنبه های کلیدی MRP، تجزیه و تحلیل نیازهای مواد اولیه است. این تجزیه و تحلیل شامل شناسایی نوع و مقدار مواد مورد نیاز برای هر مرحله از تولید است. با استفاده از داده های تاریخی و پیش بینی های آینده، MRP می تواند الگوهای تقاضا را شناسایی کرده و به مدیران کمک کند تا تصمیمات بهتری درباره خرید و نگهداری موجودی ها بگیرند.
علاوه بر این، MRP به شرکت ها این امکان را می دهد که زمان بندی تولید را بهینه کنند. با داشتن اطلاعات دقیق درباره زمان های لازم برای تامین مواد اولیه و تولید، مدیران می توانند برنامه های تولید را طوری تنظیم کنند که از حداکثر ظرفیت تولید استفاده شود و زمان های بیکاری کاهش یابد. این امر نه تنها موجب افزایش بهره وری می شود بلکه به کاهش هزینه ها نیز کمک می کند.
یکی دیگر از مزایای MRP، توانایی آن در مدیریت تغییرات است. در دنیای امروز که تغییرات سریع و غیرمنتظره در تقاضا و شرایط بازار رخ می دهد، MRP به سازمان ها این امکان را می دهد که به سرعت به این تغییرات واکنش نشان دهند. با تجزیه و تحلیل مداوم داده ها، سازمان ها می توانند برنامه های خود را به روز کرده و از بروز مشکلات احتمالی جلوگیری کنند.
با این حال، پیاده سازی MRP نیازمند دقت و توجه به جزئیات است. اطلاعات نادرست یا ناکافی می تواند منجر به برنامه ریزی نادرست و در نتیجه افزایش هزینه ها و کاهش کیفیت تولید شود. بنابراین، سازمان ها باید اطمینان حاصل کنند که داده های ورودی به سیستم MRP دقیق و به روز هستند.
در نهایت، MRP نه تنها یک ابزار برنامه ریزی است بلکه یک رویکرد جامع برای مدیریت زنجیره تامین و تولید محسوب می شود. با استفاده از این سیستم، سازمان ها قادر خواهند بود تا منابع خود را بهتر مدیریت کنند، هزینه ها را کاهش دهند و در نهایت رضایت مشتریان را افزایش دهند.
برنامه ریزی مونتاژ یکی از مراحل کلیدی در فرایند تولید است که به سازمان ها کمک می کند تا بهینه ترین روش ها را برای جمع آوری و ساخت محصولات خود شناسایی کنند. این فرایند شامل برنامه ریزی دقیق و سازماندهی مراحل مختلف تولید است، به طوری که اطمینان حاصل شود که تمام اجزا و مواد اولیه در زمان مناسب و به مقدار کافی در دسترس هستند.
در ابتدا، یکی از اصول اساسی برنامه ریزی مونتاژ، شناخت دقیق محصول و اجزای آن است. برای این منظور، لازم است که لیست دقیقی از تمام قطعات و مواد اولیه مورد نیاز برای ساخت هر محصول تهیه شود. این لیست معمولا تحت عنوان "لیست مواد" یا "BOM" (Bill of Materials) شناخته می شود. این لیست به مدیران کمک می کند تا بتوانند نیازهای مواد اولیه را شناسایی کنند و همچنین زمان بندی دقیق تری برای مراحل مختلف تولید داشته باشند.
یکی دیگر از اصول مهم برنامه ریزی مونتاژ، زمان بندی دقیق است. زمان بندی شامل تعیین زمان های لازم برای تامین هر یک از اجزا و همچنین زمان های مورد نیاز برای مونتاژ آنهاست. این امر به مدیران این امکان را می دهد که فرایند تولید را به گونه ای برنامه ریزی کنند که از حداکثر ظرفیت تولید استفاده شود و از بروز تأخیرها جلوگیری شود. در این راستا، استفاده از تکنیک های زمان بندی مانند "تکنیک مسیر بحرانی" (CPM) می تواند بسیار موثر باشد.
علاوه بر این، مدیریت موجودی نیز یکی از جنبه های کلیدی برنامه ریزی مونتاژ است. سازمان ها باید به دقت موجودی های خود را مدیریت کنند تا از کمبود یا مازاد موجودی جلوگیری شود. این کار شامل تجزیه و تحلیل داده های تاریخی و پیش بینی تقاضا برای شناسایی الگوهای مصرف و نیازهای آینده است. با استفاده از سیستم های مدیریت موجودی، شرکت ها می توانند به طور موثری موجودی های خود را کنترل کرده و از هزینه های اضافی جلوگیری کنند.
برنامه ریزی مونتاژ همچنین نیازمند هماهنگی میان بخش های مختلف سازمان است. برای مثال، بخش تامین باید با بخش تولید هماهنگ باشد تا اطمینان حاصل شود که مواد اولیه در زمان مناسب به خط تولید ارسال می شوند. همچنین، بخش فروش باید با بخش تولید همکاری کند تا پیش بینی دقیقی از تقاضا داشته باشد و بر اساس آن برنامه ریزی های لازم انجام شود. این هماهنگی می تواند به کاهش اختلالات و افزایش کارایی در فرایند تولید منجر شود.
یکی دیگر از جنبه های مهم برنامه ریزی مونتاژ، انعطاف پذیری است. در دنیای امروز که تغییرات سریع در تقاضا و شرایط بازار رخ می دهد، سازمان ها باید قادر باشند به سرعت به این تغییرات واکنش نشان دهند. برای این منظور، ایجاد سیستم های انعطاف پذیر و قابل تنظیم در فرایند مونتاژ می تواند به شرکت ها کمک کند تا بتوانند به راحتی برنامه های خود را تغییر دهند و از بروز مشکلات احتمالی جلوگیری کنند.
در نهایت، ارزیابی و بهبود مستمر فرایند برنامه ریزی مونتاژ نیز از اصول کلیدی این فرایند است. پس از اتمام هر دوره تولید، لازم است که عملکرد فرایند بررسی شده و نقاط قوت و ضعف آن شناسایی شود. این ارزیابی می تواند شامل تجزیه و تحلیل زمان های تولید، هزینه ها، کیفیت محصولات و میزان رضایت مشتریان باشد. با استفاده از نتایج این ارزیابی ها، سازمان ها می توانند فرایندهای خود را بهبود بخشند و به سمت کارایی بیشتر حرکت کنند.
به طور خلاصه، برنامه ریزی مونتاژ یک فرایند پیچیده و چندوجهی است که نیازمند دقت، هماهنگی و انعطاف پذیری بالاست. با رعایت اصول اساسی این فرایند، سازمان ها قادر خواهند بود تا محصولات خود را با کیفیت بالا و هزینه مناسب تولید کنند و در نهایت رضایت مشتریان را افزایش دهند.